The Advantages of Modular Construction
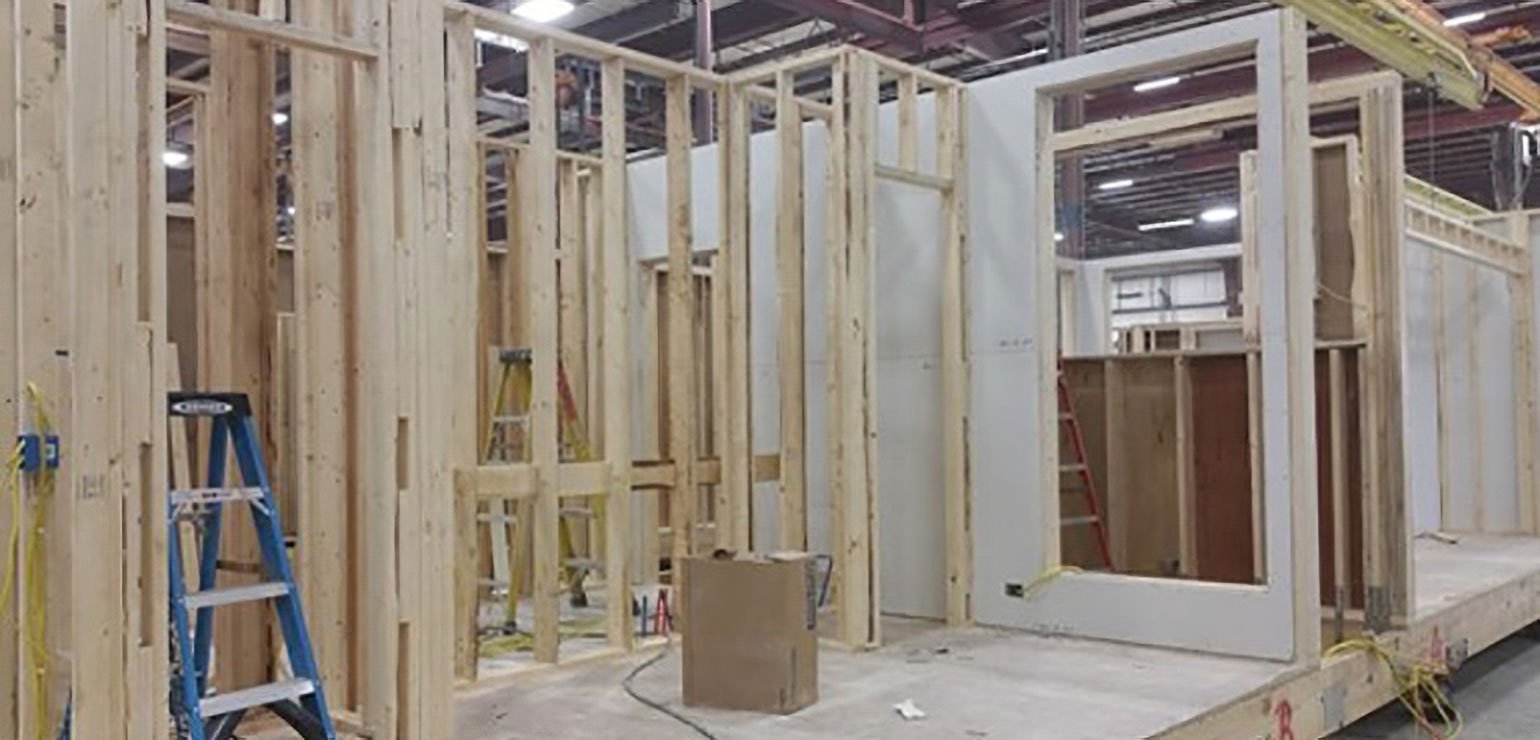
20 Jul 2021
Prefabricated Benefits for All
With skilled labor shortages, economic pressure, rising material costs, and the urgent need to reduce climate impact, the construction industry is ripe for disruption. One promising way to shake things up is the use of off-site construction, particularly modular construction. Off-site construction shifts a portion of the building processes to remote manufacturing facilities. This includes reduced time to completion, controlled environments, cost savings, reduced waste, safety and more.
Offsite activities include panel fabrication, component assembly, and modular construction, which offers maximum advantages to everyone from the building owners to occupants, to the community and environment as a whole.
- Owners: Modular construction can reduce the construction schedule by 30% - 50%, giving developers and owners a significantly faster time to occupancy. These shortened schedules can reduce risks and costs both for the construction and operation and maintenance in the future. Buildings can also prove more resilient once constructed, which can mean improved project success, lower costs, and enhanced reputation.
- Builders: Contractors using modular buildings can see reductions in weather delays, labor shortages and other disruptions that may typically occur in construction projects. The use of modular construction can also lead to optimized labor use, better coordination of trades, reduced costs and shorter schedules. Builders can retain many of these advantages and overcome geographic limitations with "pop-up" fabrication plants closer to building sites.
- Tradespeople: Construction workers may benefit from shorter, consistent commutes, but one of the biggest advantages for tradespeople is a safer, more comfortable work environment. A fabrication plant typically has better lighting, limited fall risks, fewer confined workspaces, and less heavy equipment. Additionally, reduced or eliminated exposure to extreme, variable weather contributes to a safer, more comfortable setting.
- Occupants: Occupants can benefit from healthier, more comfortable indoor environments, given better thermal and acoustic performance, reduced moisture penetration and higher air quality. Modular construction can also provide greater quantity and consistency in procurement and use of low-emitting materials and finishes. This can reduce exposure to volatile organic compounds (VOCs) and other air contaminants.
- Community: Communities often endure unpleasant impacts during construction, such as noise pollution, traffic congestion, and lower air quality. The use of modular construction limits the duration and intensity of on-site construction activities, results in fewer material deliveries and reduces construction worker commutes. All of this, in turn, diminishes negative impacts on the community.
- Environment: Modular volumes may contain additional material to give them stability for transport and lifting into place; however, this is often offset by improved efficiency in material use and significant waste reduction. Greater precision and quality control allows the building envelope to be tighter, with reduced infiltration and thermal bridging, delivering 15% to 20% energy efficiency and fewer carbon emissions. The fabrication plant can also achieve greater energy efficiency, compared to temporary heating, ventilation, and lighting on the construction site. As previously noted, reduced vehicle usage means fewer air emissions. And by their very nature, modular buildings are more adaptable and easier to relocate and reuse or recycle.
Off-site construction, especially modular building, provides multiple benefits to the construction industry, cutting costs, speeding up schedules, improving quality and performance, and reducing environmental and climate impacts. This coupled with the fact that modular allows for creative freedom and customization, illustrates how modular can provide a much-needed disruption to the industry.
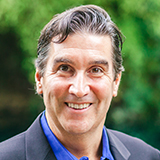
Alan Scott,
FAIA, Principal Consultant
Alan is a registered architect and sustainability expert with over 30 years of experience and a lifelong commitment to sustainability. In his early career as a practicing architect, he helped launch sustainable design practices at several major firms. Since 2000—as the 13th LEED AP—Alan has creatively applied his skills as a facilitator, consultant, project director, and teacher in support of high-performance, sustainable built environment projects across the globe. His project work focuses on boosting new and existing building performance, decarbonization, occupant wellness and resilience.